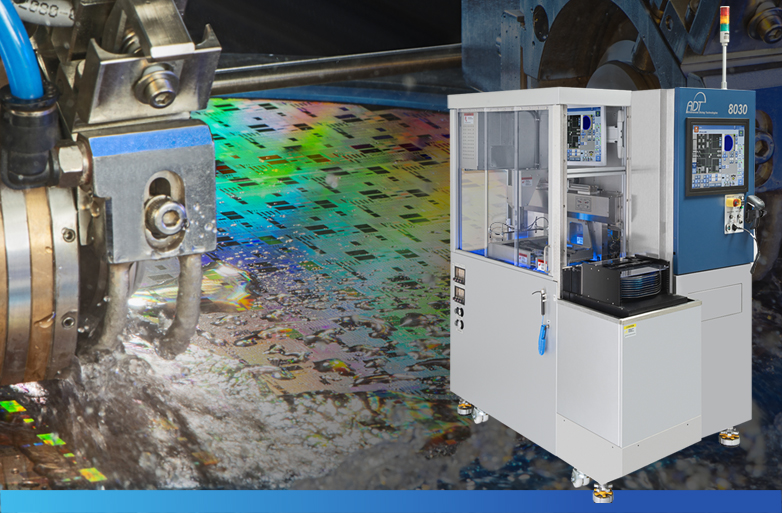
Wettable QFN PACKAGES
Following the demand from the automotive industry for chip soldering that will withstand zero faults over time, ADT developed solutions for the wettable technology.
Designed to ensure the highest safety standards for the automotive industry:
– Wettable technology for optimal soldering results
– Visible soldering allowing 100% Automated Optical Inspection (AOI)
Wettable QFN Range
Wettable QFN Dicing Saws Range
80WT
Twin spindles 2”- 3”
Tapeless for wettable flanks QFN
Silicon wafers, thin glass, QFN and BGA multi pannels
Wettable QFN Dicing Peripherals Range
WATER RECYCLING SYSTEM AR-927
Designed for closed-loop, uniform supply of cutting water
SPINDLE CHILLER 937-A
Designed for closed-loop supply of spindle cooling water